So, I am a little tweaked… I got a small bonus at work and sent a little money to my mom and daughter, got something for my wife, paid to have a tree taken out, sent Heifer and MSF some funds, paid off my last student loan (FREEDOM!!), put a little money back for a rainy day, and with the last bit decided to do a little something small just for me: I bought a few beech molding planes and 3 mortise chisels from a guy with a web store in the Scotland. I will call him UK Tool Guy. I have bought twice from him before and it all went really smooth and my purchases were exactly as expected. I bought a toothing plane from him at a good price that was in perfect working order and arrived exactly as pictured on his site.
My experience this time around was different. The order part was normal, but when I received my stuff it was all kinds of wrong. Painted parts, broken pieces, condition received was NOT as advertised, etc… I spent 4 hours cleaning and fixing and will have to spend another 4-5 repairing 2 chisels and 2 of the planes. 8-9 hours is a lot of time to unexpectedly fix stuff that I just bought. I am not super-important in the grand scheme of things, but my time is worth something to me.
Anyway, I took a few pictures and wrote the guy to let him know about the issues, asking about the possibility of some remuneration. He sends me back a mail offering me a little credit instead of a refund. I take him up on it, not knowing what the shipping will be I choose a couple of items from his web store that equals to less than £50 (~$78) that he offered up. I think my time and frustration was worth more, but I didn’t press the point.
He sent me a response that informed me that I had gone over budget and that he would “…let me off for now…” Seriously‽‽ Was this guy born with an extra set of balls? This is the third time I have done business with him. I check his site regularly for stuff I am looking for – I am even on his MF mailing list. The bottom line is that I got an unexpected crappy deal, I was gracious and completely undemanding and he will “…let me off for now…”. It took over three weeks for him to send the stuff two new items out. So much for the “Shortly” time frame he referenced in his last mail. I believe that this is the last time I will be doing business with the UK Tool Guy
For the sake of Transparency, I have included the whole chain I sent below – only deleting names and contact info.
___________________________________________________________________________
Hi Matt
Thanks for your response.
Those two items actually come to £63.50 with postage which is a bit over
£50 but I’ll let you off for now, we can maybe adjust slightly with any
future order. I will get these off to you shortly.
THANKS
> On 17 March 2015 at 11:20, drivenoutside wrote:
Hi _____,
Sorry, I didn’t mean to come off as someone that can’t be pleased. It is
not that at all and my two previous purchases were really spot on.
Thank you for your immediate response and offer for credit. I would love
to have the boxwood rule and the upholstery hammer if you are OK with that.
Thank you and regards,
Matt
> On March 16, 2015 at 4:18 AM UK Tool Guy wrote:
Hi Matt
Thanks for your e-mail and I am sorry you had so much to complain about.
Not that it is an excuse on my part but I have a funny feeling I didn’t
pack your order up as otherwise I would have picked up on some if not all
of these points as I check everything properly when I am packing it. I
understand your frustrations when you get something that is not quite what
you were expecting and once again I am sorry for this. Rather than
refunding you some monies why don’t you instead have a look at the site and
see if there is something there around the £50 mark including postage that
you might like FREE. If there is just drop me an e-mail with the product
number so I can remove it off the site and send it over to you.
THANKS
> On 15 March 2015 at 20:36, drivenoutside wrote:
Hi _____,
I received the molding planes and chisels a couple of weeks ago, but as I
travel a good bit for work, I just this weekend had the time to open the
packaging up and take a look. What I found was a little surprising as I
have ordered a couple of planes from you before and condition was spot on
as advertised. I did not expect like-new condition as some of this
material is over 200 years old, but some of it was not as stated.
Two of the collars on the sash chisels are cracked, one completely. I am
going to have to tear them apart and replace the collars. I guess I will
either see if I can source from Marples or turn down some brass stock on
the lathe.
I spent most of yesterday flattening, polishing, sharpening, and oiling
the plane blades. There is a good deal of pitting on some of them and I
will need to replace two. Most of the plane bodies were fine, but the #12
was painted red and the #16 had a screw holding a crack in the body
together. I drilled it, filled with hide glue and inserted a beech dowel.
The #1 round’s wedge is cracked in half and has been glued back together
by a previous owner. I am going to have to make a copy of it and replace.
When I unwrapped the #9 there was wood worm in the packaging. Not just old
holes, but a live worm in the plastic. There was damage to the plane and
the wedge. I took the whole lot to our local vet and had her x-ray the box
4 times. It is a Luthier’s trick and it kills any worm/moth larva.
Take a look at the attached pictures and let me know what you think and if
you think it is fair to refund me a little of the purchase price and
shipping.
Thanks,
Matt
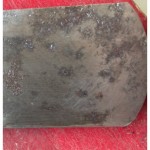
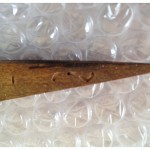
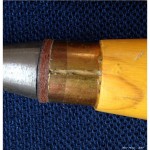
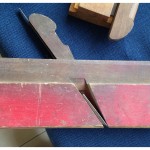
On 23 February 2015 at 15:51, drivenoutside wrote:
Hi _____,
The ship to address is: __________
My phone number is: ___________
Please send me the tracking number so that if there is a problem with the
shipper or customs, I can call right away
Thank you again,
Matt
——– Original message ——–
From: UK Tool Guy
Date:02/22/2015 2:30 PM (GMT+02:00)
To: Driven Outside
Cc:
Subject: Re: Tool Order
Hi Matt
Just written out your invoice for the tools ordered. The grand total
including postage comes to £metric shit-ton. An invoice / receipt will be included with the tools. I’m in the shop today until 4:30pm if you want to ring with card details for payment.
MANY THANKS